What is electric discharge grinding?
Table of Contents
What is electric discharge grinding?
Electrical discharge grinding (EDG) is a non-traditional thermal process for machining hard and brittle electrically conductive materials. EDG has been developed by replacing the stationary electrode used in electrical discharge machining (EDM) with rotating electrode [1-3].
What is an EDM procedure?
Electrical discharge machining (EDM) is a non-traditional machining process based on removing material from a part by means of a series of repeated electrical discharges between tools, called electrodes, and the part being machined in the presence of a dielectric fluid.
What are the applications of electric discharge grinding?

Frequently used for “one-off” tool and die production, but can be used in mass-production and transfer lines. Production rate low, i.e. aerospace applications. Many production parameters; most important are current, spark gap and frequency, dielectric type and flow rate tool (electrode) material and polarity.
Why do we choose electrical discharge diamond grinding?
The spark discharges facilitate grinding by thermally softening the work material in the grinding zone, and consequently decreasing the nromal force. It is observed that the material removal rate increases with an increase in current and pulse on-time, while it decreases with an increase in voltage and duty factor.
What is the difference between ECG and conventional grinding?
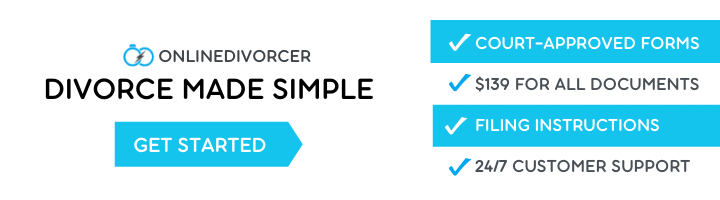
Answer: The ElectroChemical Grinding (ECG) process does not leave the typical shiny finish of abrasive grinding. This is because there is no smearing of the metal as in conventional grinding. A 16 micro inch finish or better can be achieved but it will have a matte (dull) rather than a polished look.
What type of tool we used in EDM?
Copper, copper-tungsten and brass are also extensively used as EDM tool material. Minimum tool wear condition can be obtained in EDM using graphite electrodes with frequency of about 3000 kHz, 30 A power supply. A coating of steel on graphite electrode tool is given to control the actual wear of graphite tool.
What is the principle of wire EDM?
Wire EDM machining (Electrical Discharge Machining) is an electro thermal production process where a thin single strand metal wire, along with de-ionised water (used to conduct electricity) allows the wire to cut through metal by the use of heat from electrical sparks, while preventing rust.
What are the advantages and disadvantages of EDM?
Advantages and Disadvantages EDM
- Tolerances of +/- 0.005 can be achieved.
- Material hardness does not effect process – Tungsten Carbide – Stellite – Hastelloy – Nitralloy – Waspaloy – Nimonic – Inconel all can be successfully machined by EDM.
- Cutting complex shapes and thin walled configurations without distortion.
What is the difference between electrochemical machining and electrochemical grinding?
Difference between ECM and ECG Electrochemical grinding (ECG) is similar to electrochemical machining (ECM) but uses a contoured conductive grinding wheel instead of a tool shaped like the contour of the workpiece.
Which material is used in electrochemical grinding?
There are various types of electrolytes used in electrochemical grinding such as Sodium nitrate (generally used), carbonate, hydroxide, and Sodium chloride.
How accurate is a wire EDM?
Unfortunately, there’s no simple answer. While accuracies of +/- 0.00004” (0.001mm) are sometimes quoted for wire EDM, +/- 0.0002” (0.005mm) is more widely accepted. The reality is that EDM accuracy depends on a combination of workpiece characteristics, the surface finish desired, and the time available for machining.
Which is the most frequently used tool material in EDM?
In EDM, Cu and graphite are commonly used as tool materials. The poor wear resistance is the drawback of these tools.
What are the different types of electro discharge machining?
Electric discharge machining can be divided into three common types, Die sinking EDM, Wire EDM and hole drilling EDM.
- Die sinking EDM.
- Wire EDM.
- Hole drilling EDM.
Why is wire EDM so accurate?
Speed and precision are controlled by managing cutting parameters – power and frequency – and controlling the rate of fluid flushing. Lower power and speed improve accuracy. This is because flushing moves the wire slightly, and flushing pressure is higher at higher feed rates.