What is minimum and maximum inventory level?
Table of Contents
What is minimum and maximum inventory level?
The Min/Max inventory ordering method is a basic reordering mechanism that is supported by many ERPs and other types of inventory management software. The “Min” value represents a stock level that triggers a reorder and the “Max” value represents a new targeted stock level following the reorder.
What is the maximum inventory level?
The maximum stock level is a not-to-exceed amount used for inventory planning. This stock level is based on a calculation of the cost of storage, standard order quantities, and the risk of inventory becoming obsolete or spoiling with the passage of time.
What is the difference between maximum and minimum stock level?
Maximum stock level: determined by the warehouse’s storage capacity and the purchasing or procurement policy. Minimum operating stock level: indicates the point of inventory consumption at which goods need to be replenished, just before the safety stock is used.

What are the levels of inventory?
What are the different levels of inventory?
- Minimum Level. Minimum inventory levels should be maintained at all times by a business for ensuring enough raw materials for continuing its production.
- Maximum Level.
- Danger Level.
- Average Level.
What is the importance of minimum stock level?
it helps the entity in avoiding any loss of orders that can arise due to unavailability of stock in the market, it helps the entity in keeping its obligation towards supplier very low, it helps the entity in keeping the liquidity ration in a good balance.
What do you mean by minimum level?
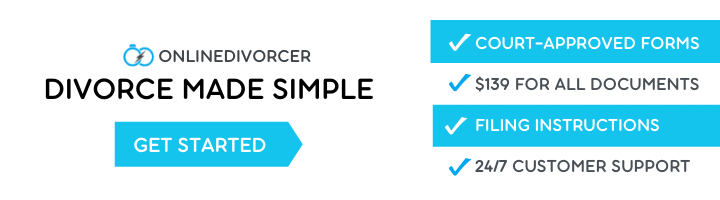
Minimum Level means the lowest level at which the entire analytical system gives a recognizable signal and acceptable calibration point for the analyte. The ML represents the lowest concentration at which an analyte can be measured with a known level of confidence.
What is a minimum stock level?
A minimum stock level is a threshold value that indicates the level below which actual material stock items should not normally be allowed to fall. In other words, a minimum stock level is a minimum quantity of a particular item of material that must be kept at all times.
What is a stock level?
Stock level means the level of stock required for an efficient and effective control of goods, to avoid over-and under-stocking of goods. The need of inventory control is to maintain the stock of goods as low as possible but at the same time make them available as and when required.
How do you set minimum inventory level?
Here it is:
- For forced-ordering and continuous review max-min systems, the formula is: Min stock level = lead time stock level + safety stock level.
- For a standard system, the formula would be: Min stock level = lead time stock level + safety stock level + review period stock level.
What is the meaning of minimum level?
Minimum Level means the lowest concentration of a substance as determined by the Department that generally can be quantified within specified limits of interlaboratory precision and accuracy under routine laboratory operating conditions in the matrix of concern.
How do you determine stock level?
FORMULA. Average Stock level = (Maximum stock level + Minimum stock level) x 14 or Minimum Stock level + 14 Reorder Quantity.
How do you find the minimum stock level in SAP?
To set this up go to Inventory > Item Master Data > Inventory Data. On this tab under Inventory Level uncheck the box by Manage Inventory by Warehouse and then you can enter numbers for Required (Purchasing UoM), Minimum, and Maximum.
What is meant by Ved analysis?
VED analysis is based on critical values and shortage cost of the item. Based on their criticality, the items could be classified into three categories: vital, essential and desirable.
What is the ROP how is it determined?
Determining ROP with safety stock This method is used by businesses that keep extra stock on hand in case of unexpected circumstances. To calculate a reorder point with safety stock, multiply the daily average usage by the lead time and add the amount of safety stock you keep.
What is roq in supply chain?
This is calculated by determining the safety stock level and the stock required to service needs during the reorder lead time. ROQ = Reorder Quantity. Again, as the name suggest, this is the quantity to be reordered when the ROP is reached.
Why are minimum and maximum inventory levels important?
Setting minimum and maximum stock levels in your computerized maintenance management system (CMMS) or inventory management database can help assure you always have immediate access to critical parts or items with long lead times, as well as providing the means to control the risk of overstocking and wasted expenditure.
What is VED and ABC analysis?
ABC and VED analysis identifies the drugs requiring stringent control for optimal use of funds and elimination of out-of-stock situations in the pharmacy.
What is FSN and VED analysis?
VED Analysis (Vital, Essential, Desirable) 3. FSN Analysis (Fast, Slow moving and Non-moving) 4. SDE Analysis (Scarce, Difficult, Easy) 5. HML Analysis (High, Medium, Low) 6.