What is pressure transducer used for?
Table of Contents
What is pressure transducer used for?
A pressure transducer is a device that measures the pressure of a fluid, indicating the force the fluid is exerting on surfaces in contact with it. Pressure transducers are used in many control and monitoring applications such as flow, air speed, level, pump systems or altitude.
What causes a pressure transducer to fail?
The pressure transducers failure causes due to issues such as multiple grounds, short circuits, improper wiring, inadequate power supply, incorrect polarity, system operation issues, and so on.
Do pressure transducers require calibration?
Calibration is critical to maintaining a pressure transducer’s accuracy and it is not a one-time process. All pressure transducers used in critical applications should be regularly calibrated to maintain high performance.

What is the difference between pressure sensor and pressure transducer?
Pressure sensors detect a force, in this case, pressure, and turn that into a continuous output signal. That signal is relative to the strength of the pressure being exerted and the type of output signal is what determines if the device is a pressure transducer or pressure transmitter.
Can transducers be repaired?
Damaged or scratched cases are replaced to make your transducer look like new. Every transducer is calibrated and tested before it is returned. Transducers are repaired at a flat rate with no hidden charges.
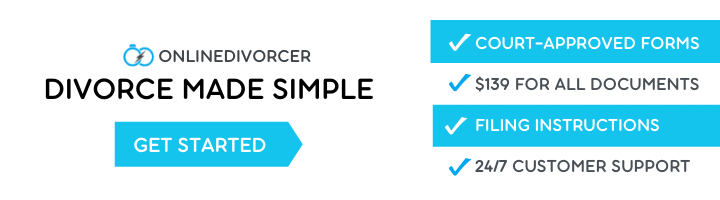
How long can a 4 to 20 mA loop be?
4-20mA loops can be used for cable runs of up to 500m, more in some cases, and offer fast response times, whilst being relatively noise immune. However, there are some important factors that you need to take into consideration in the design of your installation: The impedance of the instrument.
How do you know if you have a bad transducer?
Signs of a bad pressure transducer
- Pressure port leaks.
- Decaying output signal.
- Sudden signal changes.
- Complete loss of signal.
- Fixed output signal.
- Changes in reading accuracy.
How often should I calibrate a pressure transducer?
every four to six years
Direct-mounted pressure transmitters installed inside in a controlled environment on a process with stable conditions should be calibrated every four to six years.
How do you calibrate a pressure transducer?
To calibrate your software-controlled sensor you will need to:
- Connect the sensor to the control software.
- Accurately apply zero and full-scale pressure to the transducer.
- Using the software, adjust the zero and full-scale output calibration variables until the respective outputs of the sensor are correct.
How does a 3 wire pressure transducer work?
A three-wire sensor has 3 wires present. Two power wires and one load wire. The power wires will connect to a power supply and the remaining wire to some type of load. The load is a device that is being controlled by the sensor.
What are the 4 types of pressure?
Types of Pressure – Absolute Pressure, Gauge Pressure, Differential Pressure and Sealed Pressure.
Where are stellar technology transducers made?
Since Stellar Technology transducers are designed and manufactured in our state-of-the-art Amherst, New York, facility, we have the engineering resources and manufacturing flexibility to customize any transducer to accommodate the ever-changing test and measurement challenges faced by today’s demanding industrial environment.
What is the sensor&transducer blog?
Our blog features industry news, updates and advice to help you maximize the potential of your sensor or transducer.
How do I get a quote for a stellar technology transducer?
If you’re interested in learning more about the transducers we supply, or if you have any questions, reach out to Stellar Technology today. You can also call now to request a quote: 800.274.1846. We look forward to hearing from you!