What are some design considerations in sheet metal forming?
Table of Contents
What are some design considerations in sheet metal forming?
Below are the factors designer needs to consider while modeling a sheet metal component.
- Wall Thickness:
- Bend Radii:
- Orientation of Holes & Slots:
- K Factor:
- Bend Allowance:
- Bend Deduction:
- Bend Reliefs:
- Some Additional Features:
What factors affect selection of sheet metal materials?
Factors affecting Sheet Metal Material Selection
- Various external forces acting on the sheet metal part during its complete lifecycle.
- Weight constraints.
- Cost constraints.
- Corrosion resistance requirements.
- Assembly Process.
- Availability of material.
What are the general tolerances followed during sheet metal design?
A +/- 1 degree tolerance on all bend angles is generally acceptable in the industry. Flange length must be at least 4 times the material thickness. It is recommended to use the same radii across all bends, and flange length must be at least 4 times the material thickness.
What is the minimum hole slot distance from edge?

The minimum distance the edge of a hole should be from a form is three times the material thickness plus the bend radius. The minimum distance the edge of a hole should be from a bend is two times the material thickness plus the bend radius.
What are the design considerations of casting?
General design considerations of casting are as follows: Design of component in compression than in tension. Use of External devices for strengthen the part under tension. Provision of Fillet Radius. Avoid abrupt changes in the cross-section.
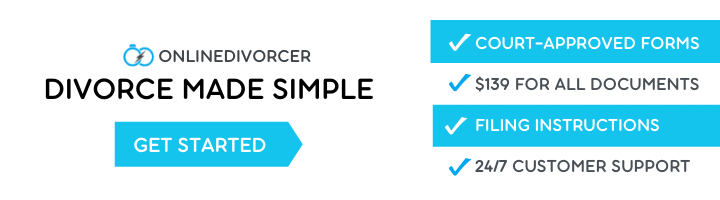
Which of the following factors are considered for selecting a material?
Many factors must be considered in materials selection, which are classified as structural, economic/business, manufacturing, durability, environmental impact, and specialist properties for unique applications.
What three factors would you consider when choosing the right metal for a job?
The Material Selection Process
- Ductility — How pliable is the material?
- Weldability — How easy is it to solder the metal?
- Machinability — Machinability refers to the ability to cut materials with a blade.
- Tensile Strength — How much force is required to snap the metal?
What is K factor in sheet metal?
In sheet metal, the K-factor is the ratio of the neutral axis to the material thickness. When a piece of metal is being formed, the inner portion of the bend compresses while the outer portion expands (see Figure 1).
What is the tolerance for sheet metal?
Confirm Tolerance, clearances, and design standards with your fabricator
Tolerance Guidelines* | |
---|---|
Edge to edge | ±0.127 mm (0.005″) |
Edge to hole | ±0.127 mm (0.005″) |
Hole to hole | ±0.127 mm (0.005″) |
Hole to hardware | ±0.254 mm (0.010″) |
What is Y factor in sheet metal?
Y factor and K factor represent part constants used in formulas to calculate the developed length of flat sheet metal required to make a bend of a specific radius and angle in a design. Y factor and K factor are defined by the location of the sheet metal material’s neutral bend line with respect to the thickness.
What are the main considerations in designing a forging?
The general guidelines to be followed in the design of forgings are discussed below:
- Keep fiber lines parallel to tensile and compressive forces and perpendicular to shear forces:
- Keep the vertical surfaces of forged parts tapered :
- Keep the parting line in one plane:
- Provide adequate fillet and corner radii:
What are the design considerations of welding?
The general principles in the design of welded assemblies
- Select the material with high weldability.
- Use of a minimum number of welds.
- Do not shape the parts based on casting or forging.
- Use standard components.
- Avoid straps, laps, and stiffeners.
- Select the proper location of the weld.
What are the 4 factors for engineering material selection?
Factors affecting the selection of materials:
- (i) Component shape:
- (ii) Dimensional tolerance:
- (iii) Mechanical properties:
- (iv) Fabrication (Manufacturing) requirements:
What are the essential factors to consider when welding?
A Dozen Factors to Consider when Welding in the Field
- Not Understanding Why the Failure Occurred.
- Incorrect Filler Metal Storage.
- Incorrect Filler Metal Handling.
- Selecting the Right Equipment.
- Choosing the Type and Diameter of Filler Metal.
- Correct Cable Sizing and Length.
- Don’t Ignore the Wire Feeder.
What are the factors needed to consider for selection of type of weld?
Selection of Joint Design: 7 Factors | Welding
- Factor # 1. Edge Distance:
- Factor # 2. Overlap:
- Factor # 3. Fit-Up:
- Factor # 4. Accessibility:
- Factor # 5. Electrode Marking or Indentation:
- Factor # 6. Welding Sections of Unequal Thicknesses:
- Factor # 7. Weld Strength: