What is FMEA in validation?
Table of Contents
What is FMEA in validation?
Failure mode and effects analysis (FMEA; often written with “failure modes” in plural) is the process of reviewing as many components, assemblies, and subsystems as possible to identify potential failure modes in a system and their causes and effects.
How can I learn FMEA?
Learning Objectives:
- Define the properties of FMEA.
- Brainstorm potential failures.
- Assess risk of failure.
- Determine areas that need action.
- Apply FMEA methods.
- Know your role for team participation.
- Apply mistake.
- proofing techniques.
What are the different types of FMEA?
Types of FMEA:

- Design FMEA (DFMEA)
- Process FMEA (PFMEA)
- Functional FMEA (FFMEA) / System FMEA (SFMEA)
- Software FMEA.
What is FMEA with example?
Failure Mode and Effects Analysis (FMEA) is a model used to prioritize potential defects based on their severity, expected frequency, and likelihood of detection. An FMEA can be performed on a design or a process, and is used to prompt actions to improve design or process robustness.
What are FMEA classes?
QC Training Services’s Failure Mode and Effects Analysis (FMEA) class is an introduction to the FMEA process within an APQP system, its planning, strategy and benefits. Learn the structure and information sources for effective use of FMEA and its correlation to the rest of the AIAG core tools.
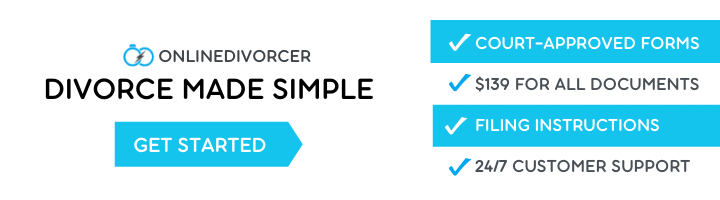
How many steps are in FMEA?
seven steps
FMEA is performed in seven steps, with key activities at each step.
What are the main elements of FMEA?
FMEA is performed in seven steps, with key activities at each step….FMEA Document Analysis
- Severity of 9 / 10 or Safety and Regulatory alone (Failure Mode Actions)
- Criticality combinations for Severity and Occurrence (Cause Actions)
- Detection Controls (Test and Control Plan Actions)
- RPN Pareto.
What is FMEA formula?
FMEA RPN is calculated by multiplying Severity (S), Occurrence (O), and Detection (D) indexes.
What is a FMEA chart?
FMEA is a qualitative and systematic tool, usually created within a spreadsheet, to help practitioners anticipate what might go wrong with a product or process.