What is 8D action plan?
Table of Contents
What is 8D action plan?
The Eight Disciplines of Problem Solving (8D) is a systematic, holistic and proven methodology designed to identify the root cause of a problem, plan a quick fix, and implement corrective actions and preventive actions to avoid their recurrence.
What is the 8D problem solving method?
Eight disciplines problem solving (8D) is a method developed at Ford Motor Company used to approach and to resolve problems, typically employed by quality engineers or other professionals. Focused on product and process improvement, its purpose is to identify, correct, and eliminate recurring problems.
What is meant by 8D?
8D stands for the 8 disciplines of problem solving. They represent 8 steps to take to solve difficult, recurring or critical problems (often customer failures or major cost drivers). The structured approach provides transparency, drives a team approach, and increases the chance of solving the problem.

What is 8D in quality control?
The eight disciplines (8D) model is a problem solving approach typically employed by quality engineers or other professionals, and is most commonly used by the automotive industry but has also been successfully applied in healthcare, retail, finance, government, and manufacturing.
How do you make an 8D report?
Your 8D report documents the below steps.
- Team approach.
- Describe the Problem.
- Containment Action.
- Root Cause Verification.
- Implement Corrective Action.
- Verify Corrective Action.
- Prevent Recurrence.
- Congratulate the Team.
How do I make an 8D report?
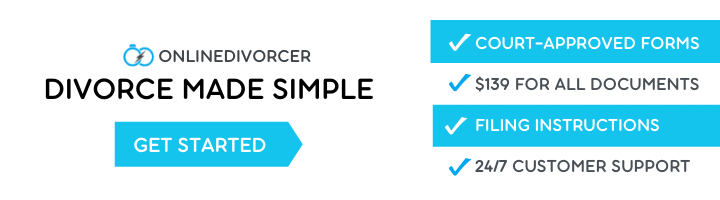
What is correction and corrective action?
Correction is taking action to correct a problem. Corrective action is action taken to correct the cause of the problem and preventing it from happening again. An example would be your child falling in the backyard and scraping their knee.
What are the 5 steps of RCA?
In order to go through the RCA process, you must be familiar with the following five steps:
- Define the problem. Analyze what you see happening, and identify the precise symptoms so that you can form a problem statement.
- Gather data.
- Identify causal factors.
- Determine the root cause(s).
- Recommend and implement solutions.
What are examples of corrective actions?
Corrective Action Examples
- Installing alarms.
- Redesigning or replacing equipment.
- Recalibrating tools.
- Updating work processes.
- Retraining employees on policies and procedures.
What is difference between corrective action and preventive action?
In simple terms, corrective action prevents recurrence, while preventive action prevents occurrence. Corrective action is carried out after a nonconformity has already occurred, whereas preventive action is planned with the goal of preventing a nonconformity in its entirety.
What are the 6 steps of RCA?
Let’s start by looking at the six steps to perform root cause analysis, according to ASQ.
- Define the event.
- Find causes.
- Finding the root cause.
- Find solutions.
- Take action.
- Verify solution effectiveness.