What is hollow shaft encoder?
Table of Contents
What is hollow shaft encoder?
A hollow shaft encoder is one of the most common shaft designs because of its versatility. Instead of having a. solid bar that has to match the motor, a hollow shaft encoder fits over the motor shaft and is then clamped in place. It’s held in position by a flexible tether.
What is the difference between an absolute and incremental encoder?
What exactly is the difference between incremental and absolute encoders? An absolute encoder can tell you the exact position of the shaft in its rotation at any given time (and how many rotations have transpired on a multi-turn absolute encoder). An incremental encoder can only report a change in position.
How do you find absolute encoder?
The test as to whether an encoder is absolute or incremental is what happens at power up. If the encoder has to move or go through some ‘wake and shake’ process to determine its position then it is incremental. If it outputs its true position without motion then it is absolute.

How does a shaft encoder work?
How does a shaft encoder work? As the motor shaft turns, a flexible coupling allows the shaft of the encoder to turn. The rotating encoder shaft passes a sensor to detect motion. Based on the shaft rotation speed and direction, the encoder then produces a square wave output used for closed loop feedback.
How do you calculate distance from encoder?
The basic calculation is Speed (m/min) = Distance per 1 pulse x Number of output pulses/ Time taken. As for HT, number of pulse per rotation is fixed as 1, Distance per pulse is Circumferential length of circumferential ring.
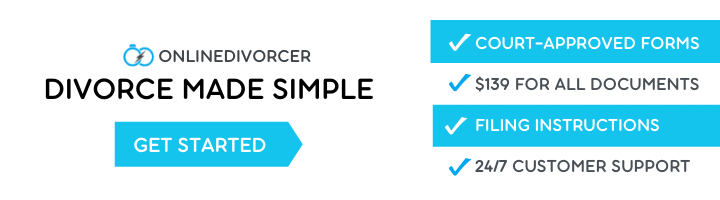
How do you calculate encoder count?
If the encoder uses X2 or X4 encoding, the encoder’s required PPR should be divided by a factor of 2 or 4, respectively. For example, if the application calls for an encoder that has a resolution of 2500 PPR, but X4 encoding is being used, then the encoder’s actual resolution only needs to be 625 PPR (2500 ÷ 4).
How do I choose encoder resolution?
Rule of thumb: The encoder resolution should be at least 2 – 4 times higher than the required position accuracy. Example: If an application demands for a 0.1° motor shaft positioning accuracy, there is typically an incremental encoder with 2048 cpt.
How is encoder accuracy calculated?
Max encoder resolution = Operating Frequency x 60 / Max RPM For example, if the encoder’s operating frequency is 125kHz and the maximum shaft speed is 1,000 RPM, the encoder ppr calculation for the maximum resolution the encoder supports is 7,500 pulses per revolution (PPR).
How do you calculate RPM from encoder?
RPM = (Frequency X 60)/ Line Count This will be our frequency, or the number of optical encoder counts that we have accumulated in one second. We then multiply that value by 60, which uses our one second total to convert to the number of pulses occurring in a minute.