How are die cast molds made?
Table of Contents
How are die cast molds made?
Die casting is a metal casting process that is characterized by forcing molten metal under high pressure into a mould cavity. The mold cavity is created using two hardened tool steel dies which have been machined into shape and work similarly to an injection mold during the process.
How do you make a permanent mold cast?
1 Permanent Mold Casting. In permanent mold casting, the molten metal is poured into the steel die and flows only at the force of gravity. For the most part, permanent mold castings are produced by pouring the molten metal into the top of a die that has been made in the desired shape of the casting.
What metal is used for die cast toys?
The majority of die-cast toys are made from zamak, which is a zinc alloy containing small amounts of aluminium and copper. An attractive feature of die-cast toy production is the ability to produce highly detailed precision models, as compared to those made from wood, plastic and sheet steel.

What materials are usually used for mold casting?
Popular casting materials include: plaster (Gypsum), resin, metal (bronze, aluminum, lead, silver and gold), and casting rubber. While there are tools specifically designed for mold making and casting, many modeling and ceramic tools are equally functional in this discipline.
What are the common material used for permanent Mould casting?
Common casting metals are aluminium, magnesium, and copper alloys. Other materials include tin, zinc, and lead alloys and iron and steel are also cast in graphite molds.
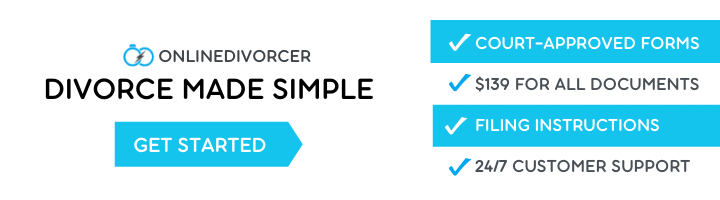
Does die cast rust?
Aluminum, zinc, and magnesium are common metal materials used for die cast metal parts. While each metal type offers corrosion resistance, the levels of rust protection vary. Less common die cast metal includes brass, copper, or other specialty alloy materials.
What are casting molds made of?
Casting molds are usually formed from gray cast iron because it has about the best thermal fatigue resistance, but other materials include steel, bronze, and graphite. These metals are chosen because of their resistance to erosion and thermal fatigue.
Which is better low pressure casting or vacuum permanent mold casting?
Vacuum permanent mold casting, however, uses vacuum pressure, which often results in better physical properties when compared to its low-pressure counterpart.