What is Step 2 in QC problem solving steps?
Table of Contents
What is Step 2 in QC problem solving steps?
- C. Step 2: Set target.
- D. Step 3: Project planning.
- E. Step 4: Root Cause Analysis.
What is quality control techniques?
Quality control ensures that defects and errors are prevented and finally removed from the process or product. Therefore, quality control should include; planning, designing, implementation, gaps identification and improvisation.
What is QC problem solving?
problem-solving activities, members follow the Plan-Do-Check-Act (PDCA) cycle, in which they. plan for improvement, implement what is planned, check and analyze what has been. implemented, and act based on the results of the checks. This problem-solving process is commonly referred to as the QC Story.
How many types of QC tools are there?

These seven basic quality control tools, which introduced by Dr. Ishikawa, are : 1) Check sheets; 2) Graphs (Trend Analysis); 3) Histograms; 4) Pareto charts; 5) Cause-and-effect diagrams; 6) Scatter diagrams; 7) Control charts.
How do you check quality?
The following steps are common among most QC inspections and are very difficult without the aid of an effective checklist to reference:
- Pulling random samples for inspection.
- Checking the product against specifications.
- Verifying packaging requirements.
- Classifying and reporting quality defects.
- Conducting on-site testing.
What are 12 steps of problem solving?
This small article attempts to explain the 12 step process.
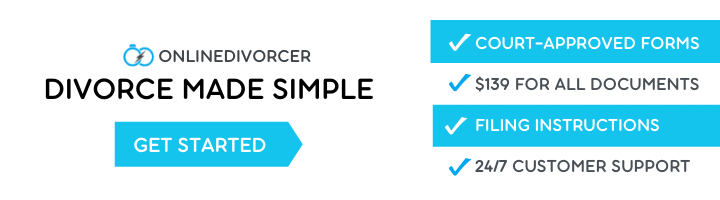
- 1) Identification of work related problem.
- 2) Selection of problem (from A list)
- 3) Defining the Problem.
- 4) Analyse the problem.
- 5) Identification of causes.
- 6) Finding the root causes.
- 7) Data Analysis.
- 8) Developing solution.
What is 7qc tools PDF?
The seven main quality tools are: the Histogram, Cause-and-Effect Diagram, Check Sheet, Pareto Chart, Flowchart, Control Charts, and the Scatter Diagram [7] .
How do you write a QC story?
QC story – Complete guide (QC story 7 steps)
- Introduction to QC Story.
- Step1: Problem Definition / Problem justification – Emergency response.
- Step 2: Observation of process – Understand the current situation.
- Step 3: Analysis: Possible causes, probable causes – Testing of hypothesis and root causes.
- Step 4: Actions.
What is QC story?
The QC Story is the name for a specific way of documenting and communicating the results of Quality Circles activities. Each QC Story shows how the circle members addressed a specific problem. Learn about the 10 steps of the QC Story and how teams use it to summarize, communicate, and learn from each other.
Why are 7 quality tools used for?
For solving quality problems seven QC tools used are Pareto Diagram, Cause & Effect Diagram ,Histogram, Control Charts , Scatter Diagrams, Graphs and Check Sheets . all this tools are important tools used widely at manufacturing field to monitor the overall operation and continuous process improvement.
What is quality circle PDF?
Quality Circle is a small group of 6 to 12 employees. doing similar work who voluntarily meet together on a. regular basis to identify improvements in their. respective work areas using various techniques for. analyzing and solving work related problems coming in.