What is continuous process improvement in TQM?
Table of Contents
What is continuous process improvement in TQM?
Continuous process improvement is defined as, “The ongoing improvement of products, services or processes through incremental and breakthrough improvements.” It doesn’t only mean that a business should make changes along the way when things aren’t working smoothly.
Is continuous improvement part of TQM?
TQM Seeks to Improve Quality and Performance This can be achieved by integrating the quality functions and key processes throughout the company. One core component of TQM is the principle of continuous improvement.
What are the 4 components of continuous improvement?

Phases of the Continuous Improvement Process (CIP)
- Phase 1 “Plan”: Plan for change and identify improvement opportunities.
- Phase 2 “Do”: Implement changes identified.
- Phase 3 “Study”: Check to determine if the change had the desired outcome.
- Phase 4 “Act”: If successful, implement it across the organization and process.
Why is continuous improvement important in TQM?
Organizations that deliver products and services of substandard quality are bound to lose out to competition. To stay ahead of the game and to keep up with the ever-changing trends in the market, they need to accept and act on the importance of continuous improvement.
Why is continuous process improvement important?
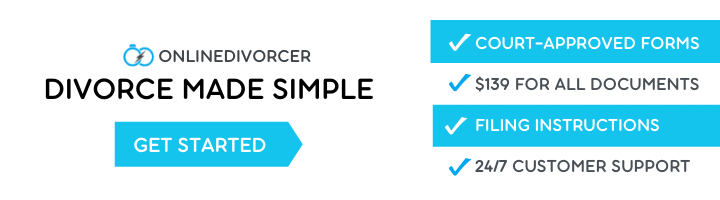
When and how to improve a business process. Process breakdowns rarely happen overnight. With continuous business process improvement, it becomes easier to isolate, identify, and resolve issues within your organization. Inefficiencies and waste are often the most important to tackle first.
Why is it important for continuous improvement in quality management?
Continuous improvement drives both the improvement of processes and products. Companies that actively look for ways to enhance their business will invariably increase the value of their products and services. This will lead to more sophisticated and overall more economically competitive offerings.
What are the key elements of continuous improvement?
Continuous Improvement
- Plan: Identify an opportunity and plan for change.
- Do: Implement the change on a small scale.
- Check: Use data to analyze the results of the change and determine whether it made a difference.
- Act: If the change was successful, implement it on a wider scale and continuously assess your results.
What are some examples of continuous improvement processes?
Here’s a look at five examples of continuous process improvement and where you can use it during your day-to-day practices:
- Ideation and Think Tanks: Initiating regular think tanks and ideation sessions can benefit your organisation.
- Surveys and Polls:
- Monthly Training:
- Time Audits:
- Catchball:
What is an example of continuous improvement?
Cross-training employees to work in a range of positions creates a continuous workplace improvement as it allows for a more smoothly run operation. Having trained staff members to step in when someone calls out sick or takes a leave of absence prevents a production slowdown.
What are continuous improvement techniques?
What is the importance of continuous improvement?
Why Continuous Improvement? Organizations dedicated to continuous improvement recognize the importance of these actions for strengthening the quality of a product, improving customer satisfaction, and for improving efficiency, productivity and profits.
Why continuous improvement process is important?
What continuous improvement means?
Continuous improvement, sometimes called continual improvement, is the ongoing improvement of products, services or processes through incremental and breakthrough improvements. These efforts can seek “incremental” improvement over time or “breakthrough” improvement all at once.
What is the benefit of continuous process improvement?
Continuous business process improvement aims to identify inefficiencies and bottlenecks and remove them to streamline workflows. In doing this, you’ll experience a wealth of benefits, including: Reduced costs. Faster processing.