What is the torque of stepper motor?
Table of Contents
What is the torque of stepper motor?
Holding torque is a measurement of how much rotating force is required to force a stationary stepper motor shaft out of position. Holding torque (T) is the product of a motor’s torque constant (KT) and the current (i) applied to the stator windings.
How do you calculate torque on a stepper motor?
To calculate load torque, multiply the force (F) by the distance away from the rotational axis, which is the radius of the pulley (r). If the mass of the load (blue box) is 20 Newtons, and the radius of the pulley is 5 cm away, then the required torque for the application is 20 N x 0.05 m = 1 Nm.
Does microstepping affect torque?
This is because microstepping allows a gradual build-up and decay of current in each motor winding, which delivers more consistent torque and, therefore, smoother motion than full-step operation. This is especially evident at slower speeds, where full-step operation causes pronounced detent torque.

What is meant by microstepping in stepper motor?
Microstepping is a way to make small steps even smaller in a stepper motor. The smaller the step, the higher the resolution and the better the vibration characteristics. In microstepping, a phase is not fully on or fully off.
Are stepper motors High torque?
Although stepper motors aren’t notable for their ability to produce high torque at high speed, it is possible, in some applications, to achieve both. The motor’s pull-out torque curve shows the maximum torque that can be produced over the range of operating speeds.
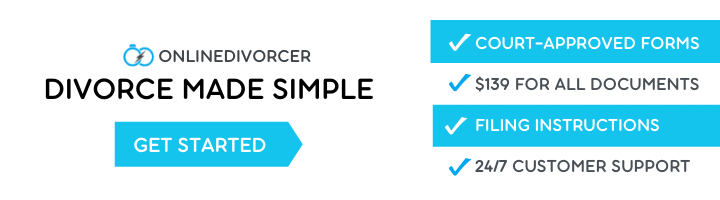
How is motor torque measured?
1) Electrical Power Meter A relatively simple method to estimate torque on the output shaft of an electrical motor is to measure its electrical power input via an electrical power meter. The meter calculates the power input by measuring the current and voltage in the line driving the motor.
How do you calculate microstepping?
Microstepping control divides each full step into smaller steps to help smooth out the motor’s rotation, especially at slow speeds. For example, a 1.8 degree step can be divided up to 256 times, providing a step angle of 0.007 degrees (1.8 ÷ 256), or 51,200 microsteps per revolution.
How does microstepping affect speed?
Microstepping decreases the size of these increments, and increases their frequency for a given rotation rate. This results in significantly smoother low speed operation.
How do you find the maximum torque of a stepper motor?
The available torque from a stepper motor falls off sharply as speed increases. The maximum torque is available when the motor is stationary. Using a higher motor power supply voltage will improve torque at higher speeds.
What is torque measured in?
The units for torque are newton-meters (Nm) or pound-feet (lb-ft). Newton (or pound) stands for the force that is acting, while meters (or feet) stand for the length of the lever arm. Another name for torque that perhaps gives a clearer indication of its meaning is rotational force.
How do you achieve microstepping in a stepper motor?
Microstepping is achieved by using pulse-width modulated (PWM) voltage to control current to the motor windings. The driver sends two voltage sine waves, 90 degrees out of phase, to the motor windings. While current increases in one winding, it decreases in the other winding.
Does microstepping reduce speed?
Do stepper motors have constant torque?
Section 1: Motor Theory A stepper motor is a constant output power transducer, where power is defined as torque multiplied by speed. This means motor torque is the inverse of motor speed.
Do stepper motors have high torque?
The motor operates by accurately synchronizing with the pulse signal output from the controller to the driver, achieving highly accurate positioning and speed control. Stepper motors feature high torque and low vibration at low-speeds, ideal for applications requiring quick positioning in short distance.
How much speed can you get with a stepper motor?
With input frequency of 1000hz, . 72 / 360 * 1000 * 60 = 120 rpm. How fast can stepper motors go? Generally speaking the top speed of a stepper motor is approximately 1000rpm. The exact speeds that are possible depend on the specific motor being used and the controller being used with it.
What is stepper motor type best for high torque?
Low cost for control achieved
How strong of a stepper motor do I Need?
While the size of a stepper motor generally dictates the low speed torque, the ability of the drive electronics to force current through the windings of the motor dictates the high speed torque.
How accurate is a stepper motor?
Steppers provide precise positioning and repeatability of movement since good stepper motors have an accuracy of 3 – 5% of a step and this error is non-cumulative from one step to the next. 8. Stepper Motors are Overload Safe. The Stepper Motor is essentially overload safe.