What is the wet end of a paper machine?
Table of Contents
What is the wet end of a paper machine?
The wet end of the paper machine is the first section of the paper machine which involves the dewatering of the pulp in slurry form. The pulp slurry is a mixture of fiber and water.
How does the Fourdrinier machine work?
Fourdrinier machine, device for producing paper, paperboard, and other fibreboards, consisting of a moving endless belt of wire or plastic screen that receives a mixture of pulp and water and allows excess water to drain off, forming a continuous sheet for further drying by suction, pressure, and heat.
What are the four sections of a Fourdrinier paper machine?
The Fourdrinier machine may be considered in four sections: wet end, press section, drier section, and calender section.

What is wet end?
Definition of wet end : the part of a paper machine between the point where the stock is fed in and the driers.
What is wet lap pulp?
: a sheet of pulp removed from a wet machine.
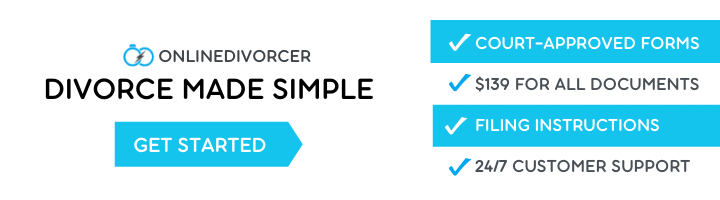
What is Fourdrinier wire?
The fourdrinier wire causes the forming of paper at the wet end of the machine. It is the section of the papermaking machine made up of a fine woven screen to let water drain away causing the pulp to remain to form a thin mat. Suction boxes remove water as the mat moves along the wire.
What are the components of paper machine?
A paper machine is divided into two main components: the wet end and the dry end. The wet end begins with the forming section. Here, the pulp mixture — 99.5 percent water and . 5 percent fiber — is spread across the forming fabric, which resembles a large mesh screen.
What is wet process in paper manufacturing?
The wet process consists of singeing, desizing, kiering, bleaching, mercerizing, and dyeing. In each stage, an appreciable amount of water is necessary for the series of operation (Rajagopalan, 1990; Pandey and Carney, 2008; Bisschops, 2003; Patel and Vashi, 2015).
How does a paper making machine work?
Modern paper-making machines are based on the principles of the Fourdrinier Machine, which uses a moving woven mesh to create a continuous paper web by filtering out the fibres held in a paper stock and producing a continuously moving wet mat of fibre. This is dried in the machine to produce a strong paper web.
What is degree Sr of pulp?
SR – higher numbers mean slower draining. CSF developed as a measure of groundwood quality. CSF decreases with refining. CSF sensitive to fines and water quality.
What is the viscosity of paper pulp?
As it is shown, no big differences were found at the end of the sequences, and all bleached pulps presented a viscosity of 650-700 g/mL. According to SCAN-C15, the degree of polymerization (DP) of cellulose can be deduced from the pulp’s viscosity. Thus, all bleached pulps had a DP in the range of 930 to 1010.
How does a paper machine work?
What is wet processing technology?
Wet-Processing is the processing stage at which textile substrate is treated with colourants and/or chemicals, collectively referred to as inputs in GOTS terminology. This includes sizing, desizing, pre-treatment, dyeing, printing (including digital printing), finishing, laundry, etc.
How many types of wet processes are there?
The wet process consists of singeing, desizing, kiering, bleaching, mercerizing, and dyeing.
What are the major components of a paper machine?
What is CSF in pulp?
Pulp Freeness Measures drainability of a pulp suspension. Canadian Standard Freeness – CSF (N. America) Schopper-Riegler – SR (Europe) CSF – higher numbers mean faster draining.
How is pulp consistency calculated?
Weigh the sample, and determine the weight of pulp fibers by subtracting the weight of the filter paper from the total sample weight. Calculate the consistency using the formula Consistency (in percent) equals the fiber weight (in grams) divided by the sample volume used (in milliliters) times 100.