What is TPM and Kaizen?
Table of Contents
What is TPM and Kaizen?
In Japanese, “kaizen” means “change for the better”, which some companies interpret as a synonym for continuous improvement. It’s closely associated with lean manufacturing and lean maintenance, as well as Total Productive Maintenance (TPM).
What is TPM in 5S?
The traditional approach to TPM was developed in the 1960s and consists of 5S as a foundation and eight supporting activities (sometimes referred to as pillars). The traditional TPM model consists of a 5S foundation (Sort, Set in Order, Shine, Standardize, and Sustain) and eight supporting pillars.
What is TPM training?
Total productive maintenance (TPM) is a team and shop floor based initiative focused on optimizing the effectiveness of manufacturing equipment. TPM helps workers efficiently care for the equipment and machines they work with, which will reduce costs, including money and space tied up with spare parts inventory.

What are the goals of TPM?
The aims of TPM are high: no breakdowns, no small stops or slow running, no defects, and no accidents. It emphasises proactive and preventative maintenance to maximise the lifespan and productivity of equipment. And it does this by empowering all employees to take responsibility for such equipment.
What is TPM example?
Total Productive Maintenance Examples Machine operators do routine cleaning, greasing, lubrication, inspections, and replacing parts. They also identify and document inspection points. Plant personnel clean their work area, removing unused tools, debris, and anything that can be considered waste.
Why do we need TPM?
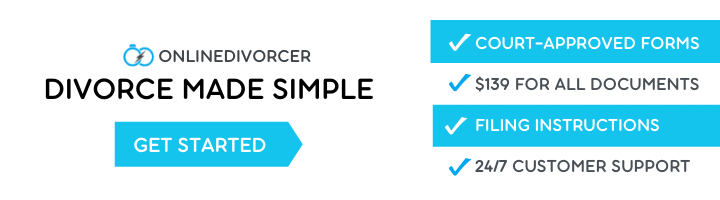
While some manufacturers may see maintenance as roadblock or hassle, TPM helps to frame maintenance as a business advantage. Implementing TPM enables manufacturers to decrease planned and unplanned downtime from breakdowns, equipment and maintenance cost, defects, and risk of damage or accidents.
What are the benefits of TPM?
5 Key Benefits of Total Productive Maintenance
- 1) Less Unplanned Maintenance and Equipment Downtime.
- 2) Lower Manufacturing Costs.
- 3) Heightened Workplace Safety.
- 4) Improved Employee Satisfaction.
- 5) Higher Quality and Fewer Defects.
What are the kaizen pillars?
The three pillars of kaizen, standardization, 5S, and elimination of waste, are critical to achieving the goals. These activities are successful only if the foundation, employee involvement is robust.
What is Kaizen rule?
Kaizen involves five key principles: know your customer, let it flow, go to gemba (or the real place), empower people and be transparent. 2. These five principles lead to three major outcomes: elimination of waste (also referred to as economic efficiency), good housekeeping, and standardization.
What are the big six losses in TPM?
SIX BIG LOSSES
- OEE AND TPM LOSSES. •
- EQUIPMENT FAILURE. •
- SETUP AND ADJUSTMENTS. •
- IDLING AND MINOR STOPS. •
- REDUCED SPEED. •
- PROCESS DEFECTS. •
- REDUCED YIELD. •
- USING THE SIX BIG LOSSES.
What are the six big losses?
The Six Big Losses: What They Are and How to Minimize Them
- Availability: Unplanned stops.
- Availability: Planned stops.
- Performance: Small stops.
- Performance: Slow cycles.
- Quality: Production rejects.
- Quality: Startup rejects.
What is TPM checklist?
This TPM checklist aims to make it easier for organizations to establish pre-requisite level requirements and successfully meet TPM criteria. Use this template to create OEE baselines for equipment and ensure training and documentation for team members.
What are the steps in implementing TPM?
We’ve summarized the steps to implementing a total productive maintenance plan and the benefits of TPM below.
- Implementing TPM.
- Step one: Identify a pilot area.
- Step two: Return equipment to its basic condition.
- Step three: Measure OEE.
- Step four: Reduce major losses.
- Step five: Implement planned maintenance.
What are the big six losses?
What are the three types of Kaizen?
The 3 Pillars of Kaizen
- Housekeeping. Housekeeping is the first pillar of Kaizen.
- Elimination of Waste. Eliminating waste is the second main pillar of Kaizen.
- Standardization. Standardization is the process of developing standards to which production is performed.