What is SAP production cost?
Table of Contents
What is SAP production cost?
SAP CO Product Costing module is used to find the value of internal cost of products. It is also used for profitability and management accounting for production. While configuring Product Costing, it involves two areas for setting − Product Cost Planning.
What is the average labor content?
Average labor utilization: The average labor utilization is defined as the total labor content divided by the sum of labor content and total idle time. If, for example, the total labor content is 30 minutes and the total idle time is 10 minutes, the average labor utilization is 30 / 40 = 0,75 = 75%.
How is service labor cost calculated?
How do you calculate labor rate? Add the full cost of what it takes an employee to create a product or complete a service. This includes their wages, taxes, and benefits. Then divide that total by the number of hours an employee works.

How do you find standard cost material in SAP?
– Enter PPC1 (standard SAP variant – configuration transaction OKKN) as the costing variant, material and plant. If you do not enter a lot size, the system uses the costing lot size from the costing view of the material master record.
How does SAP calculate actual cost?
Actual Costing is functionality provided by SAP to calculate actual prices i-e; PUP (periodic unit price) of inventories/ valuated material including Raw Material (ROH), Semi- Finished Good (HALB) and Finished Good (FERT). It includes all the actual prices for material in particular period.
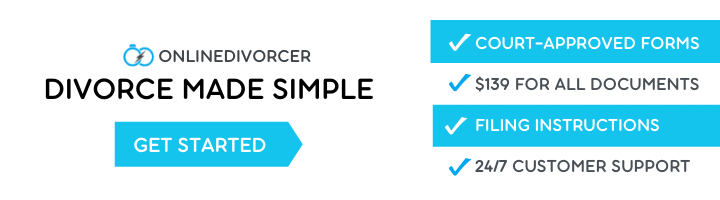
What is overhead calculation in SAP?
Overheads calculation: Overhead costing is one of the methods to allocate indirect costs to cost estimates. This involves applying a percentage or quantity-based fixed amount to a specified cost based. You can calculate: Material and production overheads.
What is a good labor utilization rate?
around 65%
On average, the direct labor utilization ratio must be around 65%. A value higher than 65% will indicate that the company is utilizing its labor force efficiently. Companies that have less paid vacations and paid training will have a lower utilization cost.
What is a good labour cost percentage?
about 30%
A common rule of thumb is that restaurants should aim to keep labor costs at about 30% of sales. However, for some restaurants that number can be lower and, for others, it needs to be higher.
What is TCode CK24 SAP?
The SAP TCode CK24 is used for the task : Price Update with Cost Estimate. The TCode belongs to the CKJ4 package.
What is the difference between moving price and standard price in SAP?
SAP recommended that, Standard price usually used for finished or semi-finished material. Moving average price are used mainly for Raw Materials and External Purchases. The Price of external procured materials varies based on Market, will reflect the current market cost.
What is standard cost and actual cost in SAP?
Difference Between Standard Cost vs Actual Cost. Standard costs are the estimated costs for products that are predetermined and arise from the units of material, labour and other costs of production for the specific time period. Actual costs refer to the costs that are actually incurred.
What is the difference between normal costing and actual costing?
Under actual costing, rates are based on costs incurred, while in normal costing, rates are based on the anticipated total efficiency of production. For example, the actual number of units produced at each rate might be lower than your team expected, resulting in inefficient use of resources and higher costs per unit.
How does SAP maintain overhead rate?
To maintain quantity-based overhead rates in the productive system, go to Transaction S_ALR_87008180 or follow the menu path, Accounting > Controlling > Product Cost Controlling > Cost Object Controlling > Product Cost by Period > Period-End Closing > Current Settings > S_ALR87008180 – Define Quantity-Based Overhead …
What is overhead in SAP PM?
Overhead costs includes all utilities costs or indirect costs. Say when you do maintenance, you may consume some electricity, water, or other items. These details can’t be captured in PM order. So Costing sheet will be defined to calculate the Overhead costs.
What is the industry average for labor cost?
The average labor cost is typically 20-35% of gross sales, depending on the industry.
What is an average labor burden percentage?
Failure to consider them can put your construction business behind with each project you take up. The labor burden lets the employer know employee costs beyond the actual wage. An employer can pay an average of 40% of the standard hourly wage. For some contractors, this cost can shoot up to 70%.
How is labor capacity calculated?
How to calculate capacity. Calculate how many total hours you will need to work on projects per week. Multiply the number of employees you have by the number of hours they work per week. (Most full-time employees in the U.S. will work for 40 hours per week.)
How can I increase my labor utilization?
5 Simple Ways to Improve Employee Utilization and Productivity
- Track your Current Productivity and Utilization.
- Analyze, Analyze, Analyze.
- Improve your Planning.
- Manage Customer Expectations.
- Create a Productive Working Environment.
- 5 Steps to Improve Employee Utilization and Productivity.