What is 8D Report example?
Table of Contents
What is 8D Report example?
The manager and team are praised for solving the problem. An 8D report example will show that Root Cause Analysis (RCA) is an integral part of the 8D process. It helps managers establish problem statements, identify potential causes, compare theories and confirm the main cause of a problem.
How do you write a good 8D report?
Your 8D report documents the below steps.
- Team approach.
- Describe the Problem.
- Containment Action.
- Root Cause Verification.
- Implement Corrective Action.
- Verify Corrective Action.
- Prevent Recurrence.
- Congratulate the Team.
How do you explain an 8D report?

8D Report: eight disciplines
- D1 – Create a team. Mobilizing a good team is essential.
- D2 – Describe the problem.
- D3 – Interim containment action.
- D4 – Identify the root cause.
- D5 – Developing permanent corrective actions.
- D6 – Implementing permanent corrective actions.
- D7 – Preventive measures.
- D8 – Congratulate the team.
How do you use the 8D method?
The 8D problem-solving process comprises these nine steps:
- D0: Prepare and plan.
- D1: Form a team.
- D2: Define and describe the problem.
- D3: Develop interim containment actions.
- D4: Define and verify root causes and escape points.
- D5: Choose and verify permanent corrective actions (PCAs) for the problem.
What are the steps in an 8D?
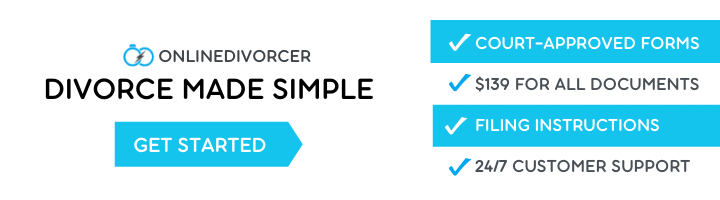
The Eight Steps of the 8D Methodology
- D0 – Plan.
- D1 – Put Together A Team.
- D2 – Define the Problem.
- D3 – Implement a Temporary Fix.
- D4 – Identify Root Causes and Chose a Solution.
- D5 – Confirm The Solution Resolves The Problem.
- D6 – Fully Implement the Solution.
- D7 – Prevent Recurrence.
How many steps are in 8D methodology?
When should you not use 8D?
While 8D problem solving is suitable for recurring problems that may repeatedly occur within a project or company, it is not ideal for simple issues that can be solved quickly by individual efforts. The process is unsuitable for a problem that can be solved with a straightforward solution.
What are the 8D quality principles?
It is a step-by-step process of identifying the root cause of a problem, providing corrective solutions, and preventive solutions to eliminate the recurring problems permanently. 8D follows the logic of PDCA (Plan-Do-Check-Adjust). And the 8D was developed and implemented in the Second World War by the US government.
Who is responsible for 8D?
Ford Motor Company developed this problem solving methodology, then known as Team Oriented Problem Solving (TOPS), in the 1980s. The early usage of 8D proved so effective that it was adopted by Ford as the primary method of documenting problem solving efforts, and the company continues to use 8D today.
What are the steps of 8D?
The Eight Steps of the 8D Methodology
- D0 – Plan.
- D1 – Put Together A Team.
- D2 – Define the Problem.
- D3 – Implement a Temporary Fix.
- D4 – Identify Root Causes and Chose a Solution.
- D5 – Confirm The Solution Resolves The Problem.
- D6 – Fully Implement the Solution.
- D7 – Prevent Recurrence.
What is a corrective action example?
Corrective Action Examples In the context of human resources, corrective actions focus on discipline. For instance, an employee who harassed a coworker may face warnings, suspension or termination. These actions aim to eliminate the cause of the harassment by reprimanding the harasser.
What is a good corrective action?
Strictly speaking, a corrective action plan is a method of documenting a problematic situation, identifying its root cause and clearly laying out a way of correcting the issue.