What is capacity utilization in manufacturing?
Table of Contents
What is capacity utilization in manufacturing?
Capacity utilization refers to how much of a factory’s production capacity is currently being utilized. The KPI tracks how much of a manufacturing operation’s potential output is being met and includes everything from machinery capacity to available resource utilization.
What increases capacity utilisation?
Improved marketing – By increasing marketing when in periods of low demand, it is likely to result in an increase in demand. This will help to increase current output thus increasing the percentage of capacity that is being utilised.
What is utilization in manufacturing?
Utilization can be defined as “how much something is used”. From a discrete manufacturing perspective, we can define utilization as “the proportion of time that manufacturing equipment is used”. Utilization is fundamentally a percentage-based metric (e.g., our current utilization is 47.62%).

How do manufacturing organizations increase capacity?
Capacity is increased either to meet an actual (immediate) increase in customer demand or an anticipated (future) increase in customer demand. Immediate capacity increases are usually achieved by: Using existing equipment for more time (Adding shifts or overtime) Using someone else’s equipment (Outsourcing)
What is meant by capacity utilization?
Capacity utilization rate measures the percentage of an organization’s potential output that is actually being realized. The capacity utilization rate of a company or a national economy may be measured in order to provide insight into how well it is reaching its potential.
Why is capacity utilization important?
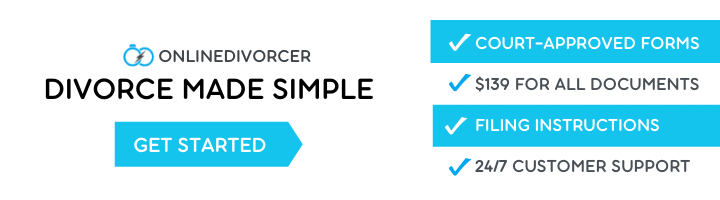
It’s an important ratio that measures the proportion of potential output to the actual realized output. Capacity utilization results in a percentage that gives insight into a company’s operational efficiency and can fluctuate based on consumer and market demand.
Why is it good to increase capacity Utilisation?
Capacity utilisation can be defined as: The percentage of total capacity that is actually being achieved in a given period. Average production costs tend to fall as output rises – so higher utilisation can reduce unit costs, making a business more competitive.
How do you increase utilization in operations management?
5 Simple Ways to Improve Employee Utilization and Productivity
- Track your Current Productivity and Utilization.
- Analyze, Analyze, Analyze.
- Improve your Planning.
- Manage Customer Expectations.
- Create a Productive Working Environment.
- 5 Steps to Improve Employee Utilization and Productivity.
How can a manufacturing company improve productivity?
5 ways to improve staff productivity
- Provide the right tools. The right tools help employees perform their tasks efficiently and on time.
- Improve the workplace environment. Ensure the work environment is geared towards productivity.
- Spend time wisely.
- Communicate effectively.
- Foster workplace culture.
How can manufacturing efficiency be improved?
How to Improve Manufacturing Efficiency
- Don’t Waste Material. Waste is a broad term, and can refer to materials, energy, man-hours or space.
- Improve Training.
- Quantify Everything.
- Organize Everything.
- Standardize Work.
- Implement Cellular Manufacturing.
- Proactively Manage Equipment Failures.
- Strengthen Your Supply Base.
Why is high capacity Utilisation good?
What does high capacity Utilisation mean?
Capacity utilisation is a measure of the extent to which the productive capacity of a business is being used. It can be defined as: The percentage of total capacity that is actually being achieved in a given period.
Why is it good to increase capacity?
It can: Decrease per-unit cost and improve profit margins. Help gain labour economies of scale (particularly useful for businesses with challenges keeping skilled staff) Potentially decrease energy costs.
How does capacity utilisation affect quality?
However, when capacity utilization passes its maximum due to demand that exceeds your ability to supply the products, your costs rise and product quality decreases. To meet excess demand, you have to schedule overtime that results in higher costs and stressed workers who make more mistakes.
What are the 5 steps to increasing capacity?
To help you tackle these complexities, here are 5 key strategies for improving operational capacities.
- Measure Existing Capacity Through Digitization.
- Create Cyber-Physical Manufacturing Ecosystems via IIoT Adoption.
- Implement Proactive Maintenance Scheduling.
- Fine Tune Production Planning Using S&OE.
What is capacity Utilisation?
Capacity utilization refers to the manufacturing and production capabilities that are being utilized by a nation or enterprise at any given time. It is the relationship between the output produced with the given resources and the potential output that can be produced if capacity was fully used.
How can manufacturing operational efficiency be improved?
Increase Operational Efficiency With These 6 Steps
- Implement and increase automation.
- Maintain a focus on safety.
- Train and retrain.
- Keep up with maintenance.
- Review the facility floor layout.
- Define goals.
What are the methods to improve productivity?
15 Ways to Increase Productivity at Work
- Track and limit how much time you’re spending on tasks.
- Take regular breaks.
- Set self-imposed deadlines.
- Follow the “two-minute rule.”
- Just say no to meetings.
- Hold standing meetings.
- Quit multitasking.
- Take advantage of your commute.
How can you increase productivity?
Try incorporating these tips to increase that productive flow and work smarter!
- Stop multitasking. It can be tempting to want to take care of a few tasks at once, especially if they seem small or easy.
- Take breaks.
- Set small goals.
- Take care of the biggest tasks when you’re most alert.
- Implement the “two-minute rule”
How does high capacity Utilisation help improve profitability?
Average production costs tend to fall as output rises – so higher utilisation can reduce unit costs, making a business more competitive. The main reason for this is that total fixed costs in the short run can be spread over a higher level of sales / output.